Comprehensive Guide: What is Porosity in Welding and How to Prevent It
The Scientific Research Behind Porosity: A Comprehensive Overview for Welders and Fabricators
Comprehending the intricate systems behind porosity in welding is vital for welders and fabricators making every effort for impressive craftsmanship. From the make-up of the base products to the intricacies of the welding process itself, a plethora of variables conspire to either worsen or alleviate the visibility of porosity.
Recognizing Porosity in Welding
FIRST SENTENCE:
Examination of porosity in welding discloses critical insights right into the stability and top quality of the weld joint. Porosity, characterized by the visibility of tooth cavities or spaces within the weld steel, is an usual worry in welding procedures. These gaps, otherwise appropriately addressed, can endanger the structural honesty and mechanical homes of the weld, causing prospective failings in the ended up item.

To find and evaluate porosity, non-destructive screening methods such as ultrasonic testing or X-ray examination are commonly used. These techniques permit the identification of inner flaws without compromising the honesty of the weld. By evaluating the size, form, and circulation of porosity within a weld, welders can make informed decisions to improve their welding procedures and achieve sounder weld joints.

Factors Influencing Porosity Formation
The incident of porosity in welding is affected by a myriad of factors, ranging from gas protecting performance to the intricacies of welding specification setups. Welding parameters, consisting of voltage, existing, travel speed, and electrode type, likewise influence porosity development. The welding method utilized, such as gas metal arc welding (GMAW) or protected metal arc welding (SMAW), can affect porosity development due to variations in warm distribution and gas protection - What is Porosity.
Results of Porosity on Weld High Quality
The visibility of porosity likewise damages the weld's resistance to deterioration, as the caught air or gases within the voids can respond with the surrounding atmosphere, leading to degradation over time. Furthermore, porosity can hinder the weld's ability to withstand stress or impact, more endangering the overall top quality and dependability of the welded framework. In essential applications such as aerospace, vehicle, or structural building and constructions, where security and durability are extremely important, the harmful results of porosity on weld high quality can have extreme consequences, stressing the significance of decreasing porosity with correct welding techniques and treatments.
Strategies to Lessen Porosity
To enhance the high quality of welded joints and make sure architectural stability, welders and fabricators utilize details techniques aimed at minimizing the development of spaces and dental caries What is Porosity within the material during the welding procedure. One reliable method to lessen porosity is to make certain appropriate product prep work. This includes comprehensive cleansing of the base steel to remove any pollutants such as oil, oil, or moisture that might add to porosity development. In addition, using the suitable welding criteria, such as the appropriate voltage, present, and take a trip rate, is essential in preventing porosity. Keeping a regular arc size and angle throughout welding likewise aids lower the chance of porosity.

Furthermore, selecting the right shielding gas and maintaining proper gas flow rates are important in reducing porosity. Utilizing the suitable welding method, such as back-stepping or utilizing a weaving movement, can also help distribute heat evenly and reduce the possibilities of porosity formation. Lastly, ensuring proper air flow in the welding atmosphere to remove any possible resources of contamination is important for accomplishing porosity-free welds. By carrying out these methods, welders can effectively minimize porosity and generate top notch welded joints.
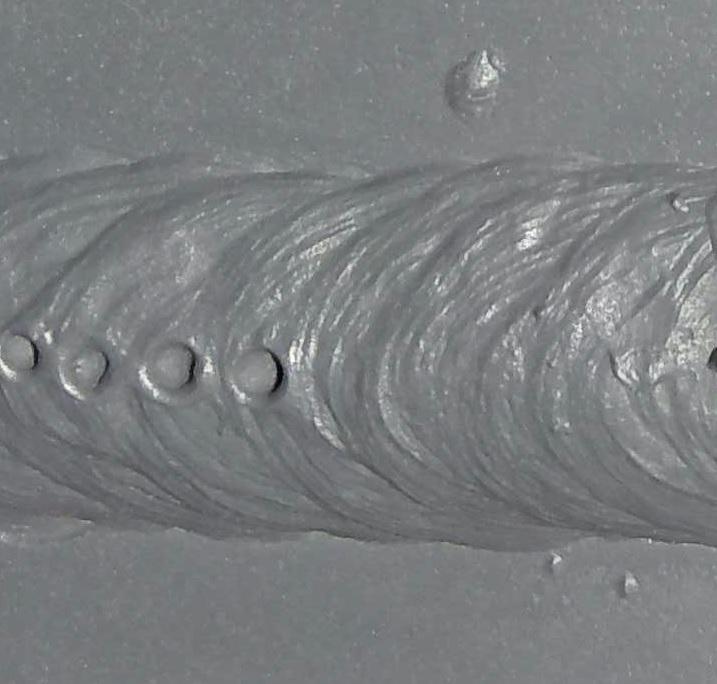
Advanced Solutions for Porosity Control
Implementing cutting-edge modern technologies and ingenious techniques plays a critical duty in attaining remarkable control over porosity in welding procedures. One sophisticated remedy is using innovative gas blends. Shielding gases like helium or a combination of argon and hydrogen can aid decrease porosity by providing far better arc security and enhanced gas insurance coverage. Additionally, using sophisticated welding strategies such as pulsed MIG welding Home Page or customized atmosphere welding can additionally assist minimize porosity issues.
Another advanced option involves making use of innovative welding equipment. Making use of equipment with integrated features like waveform control and sophisticated power resources can boost weld high quality and decrease porosity dangers. Additionally, the execution of automated welding systems with precise control over specifications can dramatically minimize porosity problems.
In addition, including advanced monitoring and assessment innovations such as real-time X-ray imaging or automated ultrasonic testing can aid in spotting porosity early in the welding process, enabling for instant restorative resource actions. Overall, integrating these sophisticated services can substantially enhance porosity control and improve the general high quality of welded elements.
Final Thought
In verdict, understanding the scientific research behind porosity in welding is vital for welders and makers to generate top notch welds - What is Porosity. Advanced services for porosity control can even more boost the welding procedure and make certain a strong and trusted weld.